Hydraulic cylinders are the undisputed champions among industrial giants. These powerful actuators convert fluid pressure into linear motion, driving everything from colossal construction equipment to the delicate movements of robotic arms. But even these titans can succumb to failure, disrupting operations and causing costly downtime.
This article delves into the reasons why hydraulic cylinders fail and explores the critical concept of synchronisation in multi-cylinder systems. By understanding these potential pitfalls, you can ensure your hydraulic systems operate with smooth efficiency and achieve true “hydraulic harmony.”
Hydraulic Cylinder Failures
- Internal Leakage: Over time, wear and tear on seals can cause internal leakage within the cylinder. This can lead to reduced force output, erratic speed control, and difficulty maintaining position.
- External Leakage: External leaks can occur at the cylinder rod seal, fittings, or hoses. This can lead to a loss of hydraulic fluid, reduced system pressure, and potential environmental hazards.
- Bent or Damaged Rod: The piston rod is a critical component of the cylinder, and it can become bent or damaged due to excessive side loading, impact, or corrosion. A damaged rod can compromise sealing, reduce efficiency, and even cause catastrophic failure.
- Cylinder Fatigue: Hydraulic cylinders are designed to withstand specific loads and pressures. However, if a cylinder is repeatedly subjected to excessive loads or pressures, it can eventually fatigue and fail.
- Contamination: Contamination of the hydraulic fluid with dirt, debris, or moisture can accelerate wear and tear on components, lead to internal blockages, and contribute to corrosion.
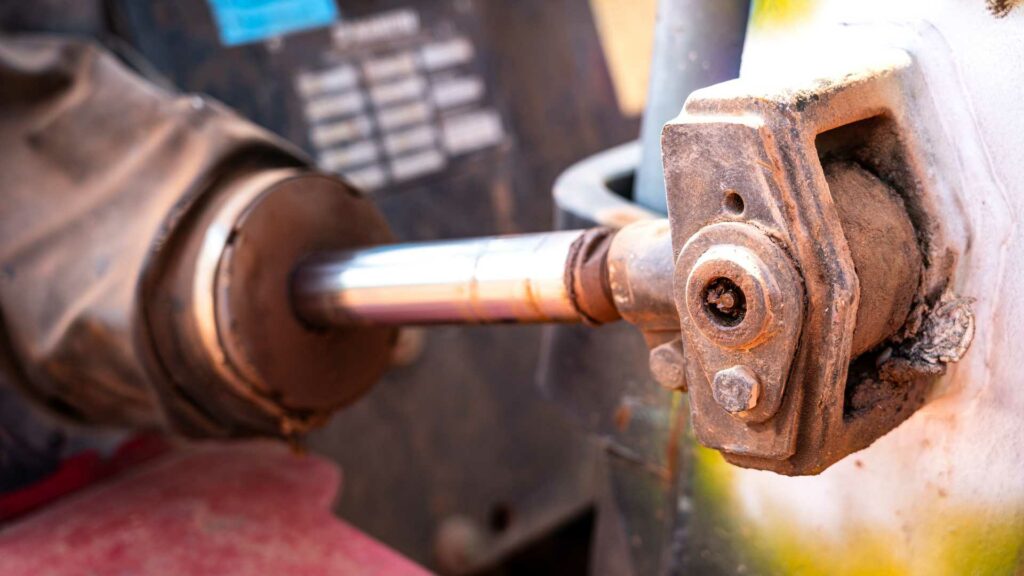
Cylinders Working Together Out of Sync
- Unequal Load Distribution: If the cylinders are lifting or pushing uneven loads, this can cause flow and pressure differences that push one cylinder ahead of the other.
- Air in the System: The presence of air in the hydraulic system can cause erratic movement and prevent cylinders from extending or retracting at the same rate.
- Contamination: As mentioned previously, contamination in the hydraulic fluid can increase friction and impair smooth cylinder operation.
- Valve Issues: Malfunctioning or improperly adjusted directional control valves can lead to uneven flow rates between cylinders, causing them to get out of sync.
- Flexible Hose Distortion: Hoses that are not properly sized or routed can distort under pressure, causing alignment issues and affecting synchronised movement.
- Loose Mountings: If the cylinders are not securely mounted and aligned, this can allow for slight movements that throw them out of sync.
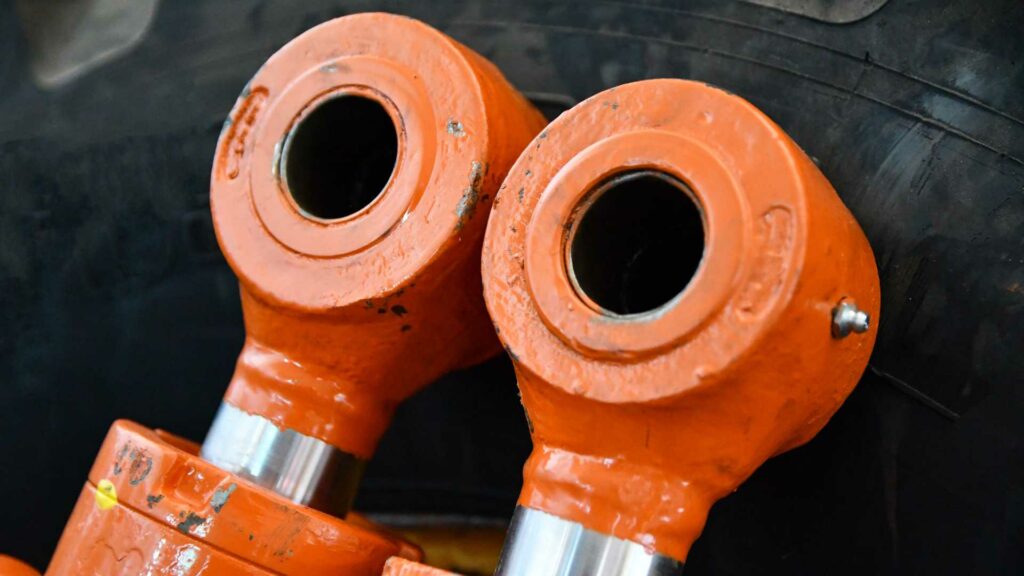
Common Causes of Hydraulic Cylinder Failure and Desynchronisation
By understanding these common causes of failure and desynchronisation, hydraulic system operators and maintenance personnel can take steps to prevent these issues and ensure the smooth, efficient operation of their equipment. This can involve regular inspections, preventive maintenance practices, proper system design, and using high-quality components.
The Synchronicity Challenge: Keeping Cylinders in Harmony
When multiple hydraulic cylinders work together to perform a coordinated task, maintaining synchronisation is crucial. Even minor discrepancies can lead to jerky movements, reduced accuracy, and potential damage to equipment. Here’s how to ensure your cylinders perform their ballet in perfect unison:
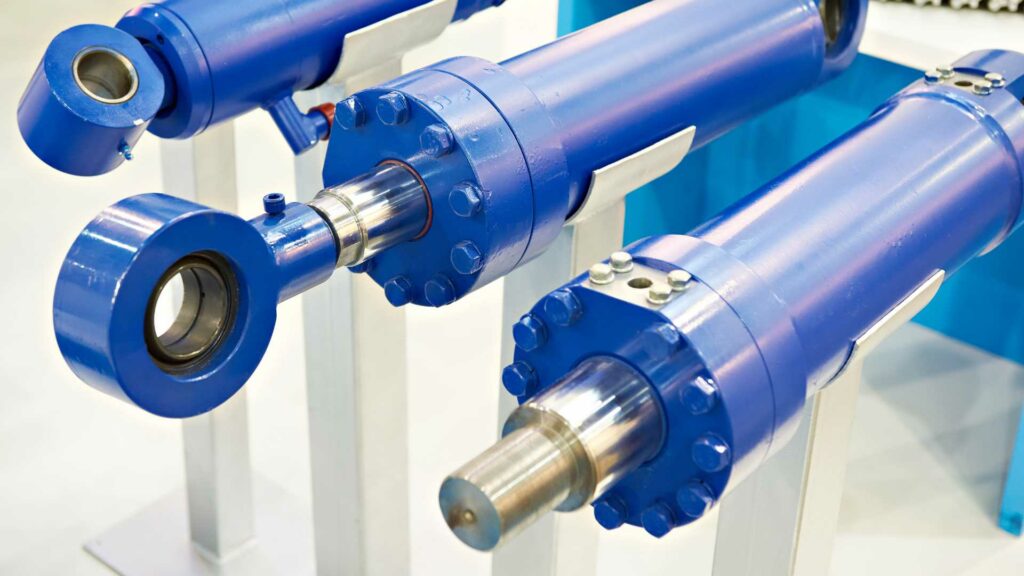
Identical Twins: Matched Components for Seamless Performance
Ensure cylinders used in tandem have identical specifications, including bore size, stroke length, and flow rates. Slight variations can lead to inconsistencies in performance.
Flow Rate Finesse: Achieving Balanced Flow
Balanced flow rates are essential for synchronised movement. Use flow dividers or metering orifices to ensure each cylinder receives an equal volume of fluid. Consistent flow translates to consistent movement.
Pressure Perfecting: Compensation for External Influences
External factors like friction and uneven loads can cause pressure variations between cylinders. Pressure compensation valves automatically adjust pressure to maintain equal force across all cylinders, ensuring a unified movement.
Rod Alignment: A Straight Path to Success
Precise alignment of cylinder rods is critical. Misalignment can cause binding and uneven extension or retraction, leading to jerky movements and potential damage. Double-check rod alignment during installation and maintenance to avoid synchronisation issues.
High-Tech Harmony: Electronic Synchronisation for Demanding Applications
For highly precise applications, electronic synchronisation systems can be employed. These systems use sensors and feedback loops to continuously monitor and adjust cylinder positions in real-time, ensuring perfect coordination even under demanding conditions.
Honing Your Hydraulic Expertise
By understanding the common causes of hydraulic cylinder failure and the importance of synchronisation, you can take proactive steps to optimise your hydraulic systems. Here at Honingcraft, we are your one-stop shop for all your hydraulic needs.
We offer a comprehensive range of high-quality hydraulic components, from cylinders and seals to valves and fluids. Additionally, our team of experts boasts extensive knowledge and experience in hydraulic system design, maintenance, and troubleshooting. Contact us today!