When selecting a tube for hydraulic cylinders, construction projects, or industrial applications, understanding the difference between seamless tubes and welded tubes is essential. Both types serve critical roles, but they differ in manufacturing processes, applications, and performance characteristics. This guide will unpack the distinctions to help you choose the right type for your specific needs.
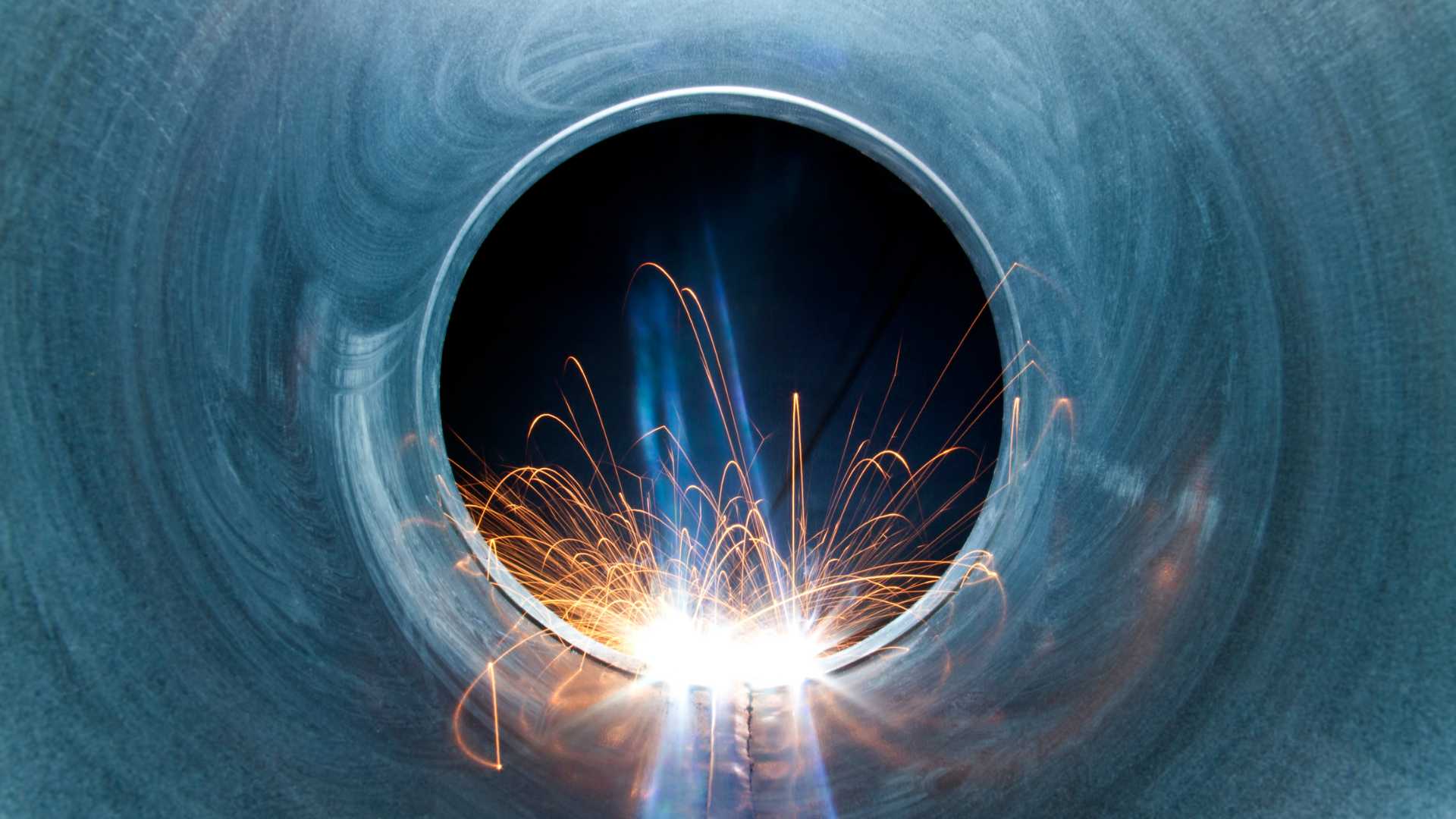
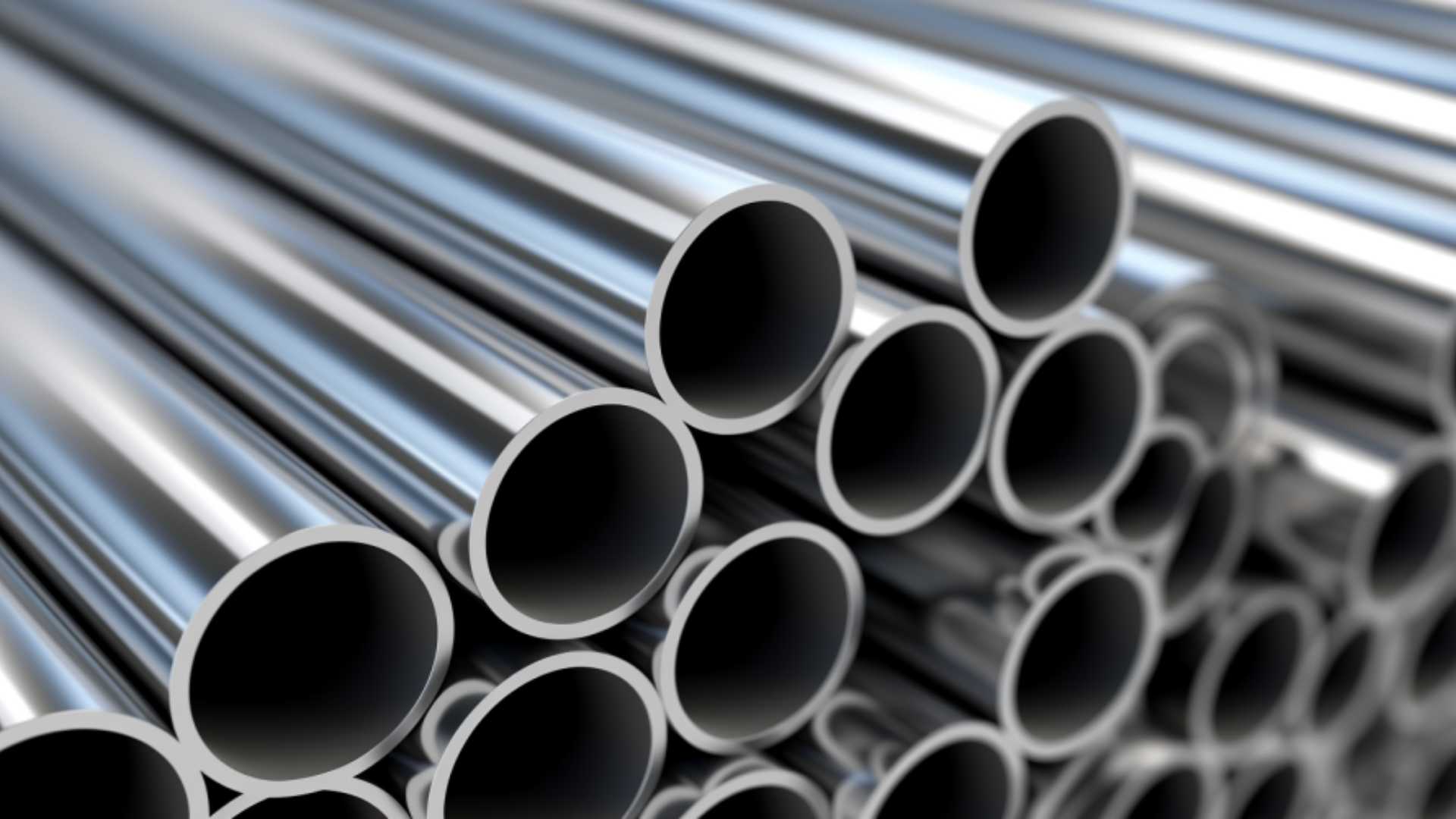
1. Manufacturing Process: The Foundation of Difference
Seamless Tubes
Seamless tubes are manufactured through a process that does not involve welding or seams. A solid cylindrical piece of steel, known as a billet, is heated and pierced to create a hollow tube. The resulting tube is then elongated and shaped into the desired dimensions through rolling and drawing processes.
This seamless structure ensures the tube has no weak points, making it a preferred choice for high-pressure applications.
Welded Tubes
Welded tubes, as the name implies, are produced by rolling a flat sheet of metal (strip or plate) into a cylindrical shape and then welding the edges together. The weld seam is typically inspected and treated to ensure the tube meets quality standards. These tubes are often cold-formed after welding to improve their mechanical properties.
2. Seamless vs. Welded Tubes at a Glance
Below is a comparison table summarising the key differences between seamless and welded tubes:
3. Applications of Seamless and Welded Tubes
The table below highlights the specific applications for each type of tube:
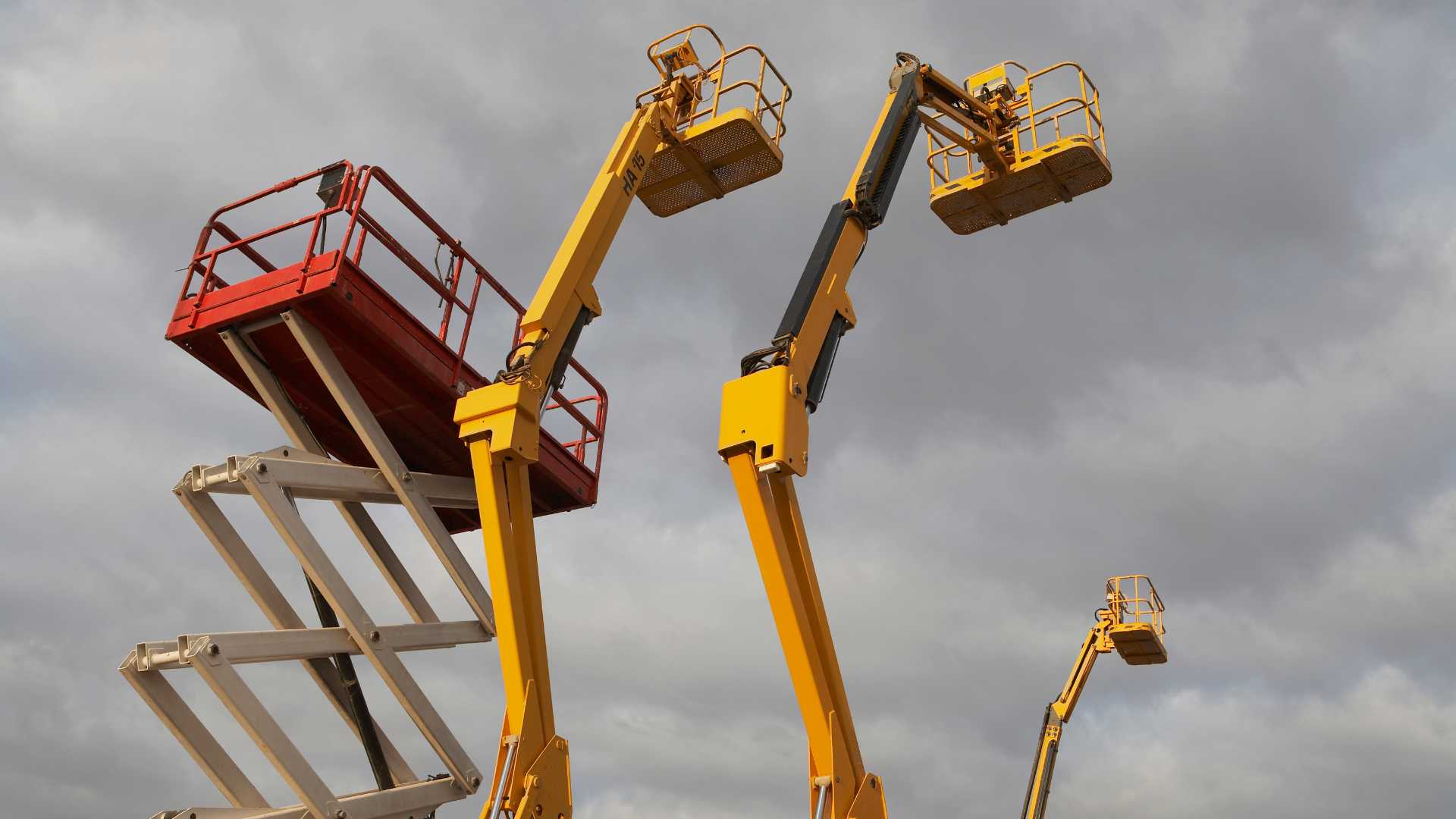
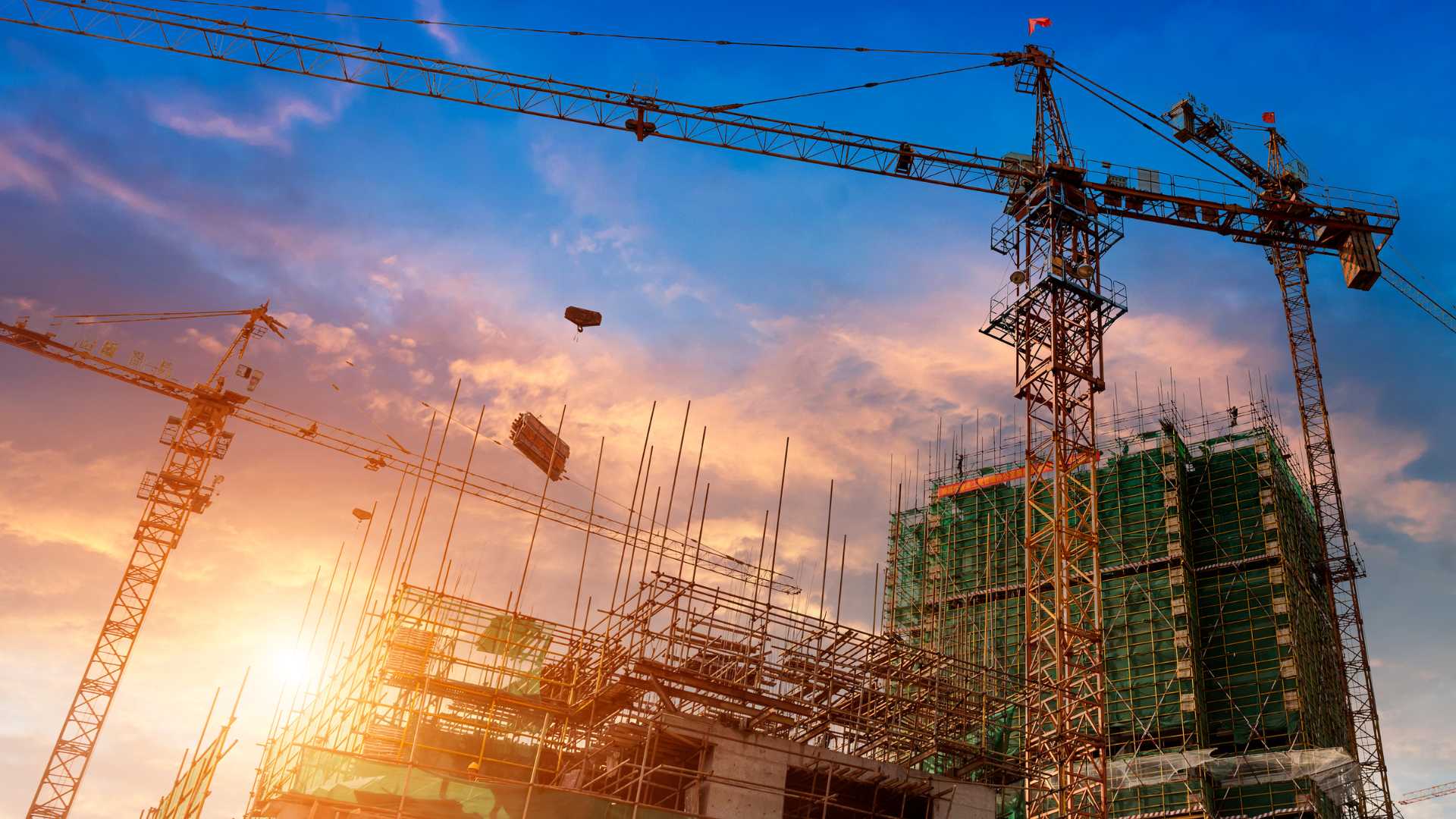
4. Structural Strength and Durability
Seamless Tubes: Superior Strength
Seamless tubes are inherently stronger due to their uniform structure. With no weld seam, there is no inherent weak point, which makes them highly resistant to pressure and mechanical stress. This feature is crucial in industries like hydraulics, where cylinders must withstand intense pressures without the risk of rupture or failure.
Welded Tubes: Reliable but Limited by the Weld
The strength of a welded tube largely depends on the quality of the weld. Modern welding techniques have minimised disparities in strength between the seam and the tube body, but a seam still introduces a potential point of weakness under extreme conditions. For applications involving lower pressure or stress, welded tubes perform effectively and economically.
Making the Right Choice for Your Application
- Pressure Requirements: Seamless tubes are better for high-pressure applications.
- Budget Constraints: Welded tubes are more cost-effective for standard uses.
- Precision Needs: Seamless tubes deliver superior uniformity and smoothness.
- Lead Times: Welded tubes are easier to source and customise.