Honing and Roller Burnishing are two of the most prominent techniques used for finishing the interior surfaces of cylindrical components, each offering unique advantages depending on the application. These processes are widely utilised in industries where surface finish and dimensional accuracy are critical to the performance and longevity of components. While both techniques aim to improve the quality of a component’s surface, their methods, applications, and outcomes differ significantly, making them suitable for different purposes and production scenarios.
Understanding the differences between honing and roller burnishing is essential when deciding which process to use for your specific requirements. In this article, we’ll break down the fundamental distinctions between honing and roller burnishing, helping you choose the technique that aligns with your industrial needs and production goals. Whether you prioritise precision, efficiency, or surface characteristics, knowing when to use each method can significantly impact the performance and cost-effectiveness of your components.
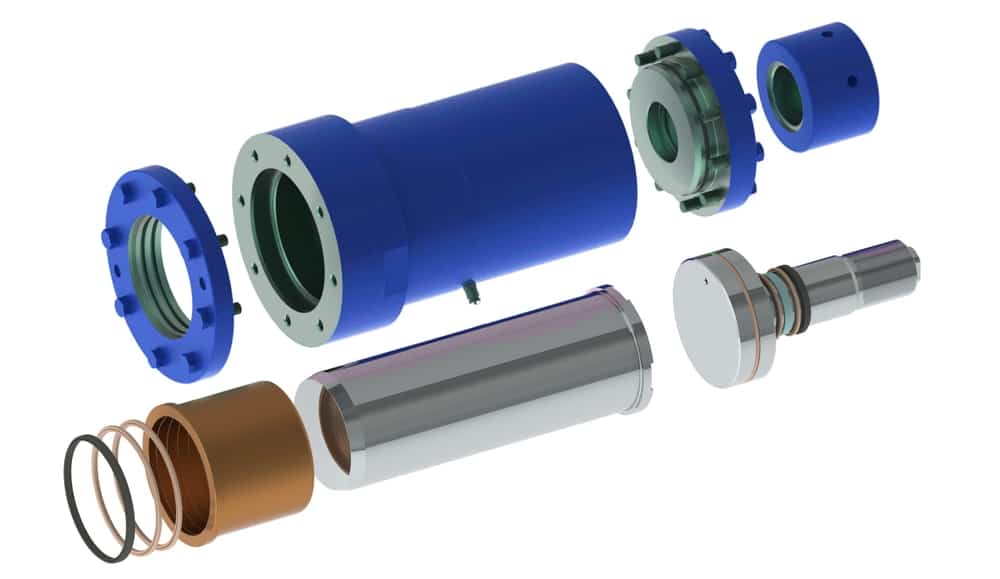
What is Honing?
Honing is a material removal process that uses an abrasive tool to create a precision surface on a metal component. The process involves rotating abrasive stones pressed against the cylinder’s surface while being moved in a reciprocating motion. This results in a crosshatch pattern that enhances lubrication retention and improves the component’s performance under load.
Key Benefits:
- Precision: Achieves high dimensional accuracy and fine tolerances.
- Surface Texture: Produces a crosshatch pattern for better lubrication and wear resistance.
- Versatility: Suitable for hard metals and irregular materials.
Applications:
- Hydraulic cylinders
- Engine cylinders
- Pneumatic systems
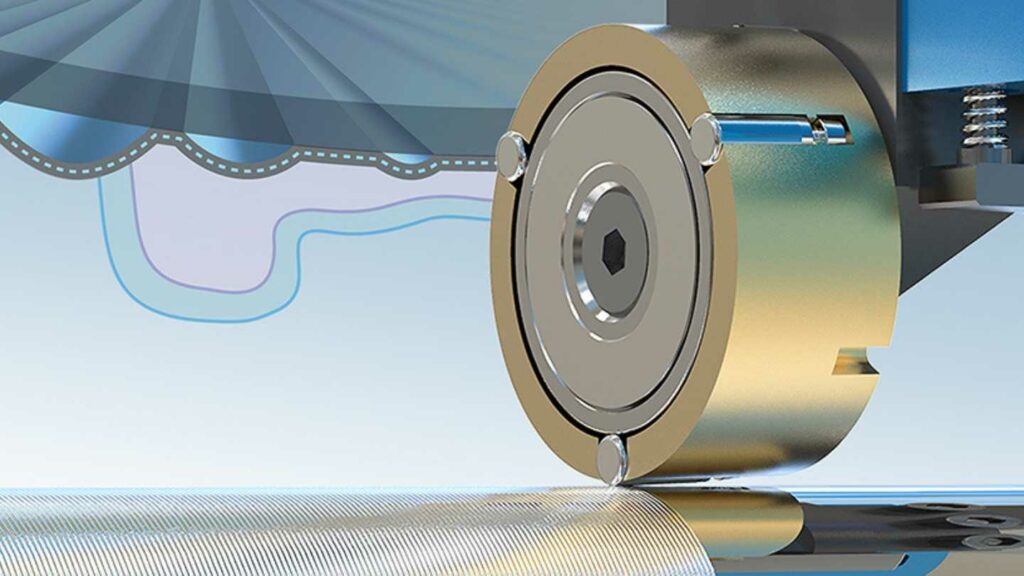
What is Roller Burnishing?
Roller burnishing is a non-abrasive finishing process that uses smooth, hardened rollers to deform the surface of a cylindrical component plastically. The applied pressure smooths out surface peaks and fills in valleys, resulting in a polished finish without removing material. This process improves the surface finish and increases hardness through work hardening.
Key Benefits:
- Efficiency: Fast and cost-effective for high-volume production.
- Surface Hardening: Improves surface hardness without altering dimensions.
- Eco-Friendly: Produces no waste or debris.
Applications:
- Shafts
- Pistons
- Bearings
Honing vs. Roller Burnishing: A Comparison
Aspect | Honing | Roller Burnishing |
Process Type | Abrasive material removal | Surface plastic deformation |
Material Removal | Removes a small amount of material | No material removed |
Surface Finish | Creates a crosshatch pattern | Produces a smooth, mirror-like finish |
Dimensional Accuracy | High precision with adjustable tolerances | Improves surface without significantly altering dimensions |
Speed | Relatively slower process | Fast and efficient |
Suitability | Ideal for hard metals and critical tolerances | Best for softer metals and high-production scenarios |
Environmental Impact | Generates waste (abrasive debris) | No waste or debris |
Choosing the Right Process
- Surface Finish Requirements: If you need a textured surface for lubrication retention, honing is the better choice. For a polished, mirror-like finish, opt for roller burnishing.
- Material Characteristics: Honing is more effective for hard metals, while roller burnishing is suitable for softer materials.
- Production Volume: For high-volume production with tight timelines, roller burnishing is faster and more cost-efficient. Honing, on the other hand, is ideal for precision, low-volume applications.
- Tolerance Needs: If dimensional accuracy and specific tolerances are critical, honing is the way to go.
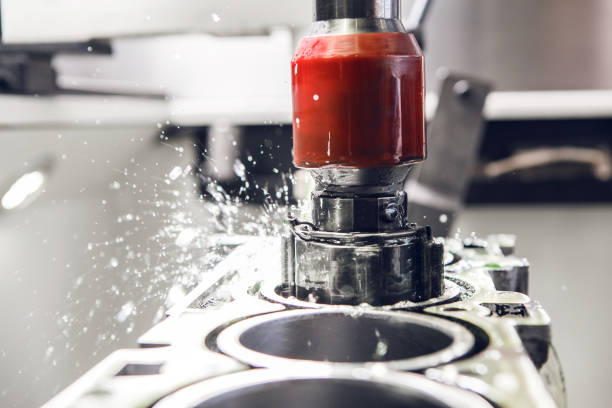
Enhance Your Component Performance with Honingcraft
At Honingcraft, we specialise in delivering top-notch honing and roller-burnishing solutions tailored to your unique needs. Whether you require precision honing for hydraulic cylinders or efficient roller burnishing for high-production components, our team of experts is here to help.
Contact us today to learn more about our services and discover how we can help you achieve superior surface finishes that enhance the durability and performance of your components.
📞 Call us now at: +27 11 824 6010
📧 Email us at: info@honingcraft.co.za
🌐 Visit us at: www.honingcraft.co.za
Transform your manufacturing process with Honingcraft – your trusted partner in precision engineering.