Cylinder rods are the workhorses of many machines, guiding pistons and transferring force within a hydraulic or pneumatic system. Their performance directly impacts the efficiency and lifespan of your equipment. Selecting the right material and surface treatment for your cylinder rods is crucial to ensure their durability, wear resistance, and smooth operation. This article explores the factors to consider when choosing cylinder rod materials and treatments, along with a table outlining common options.
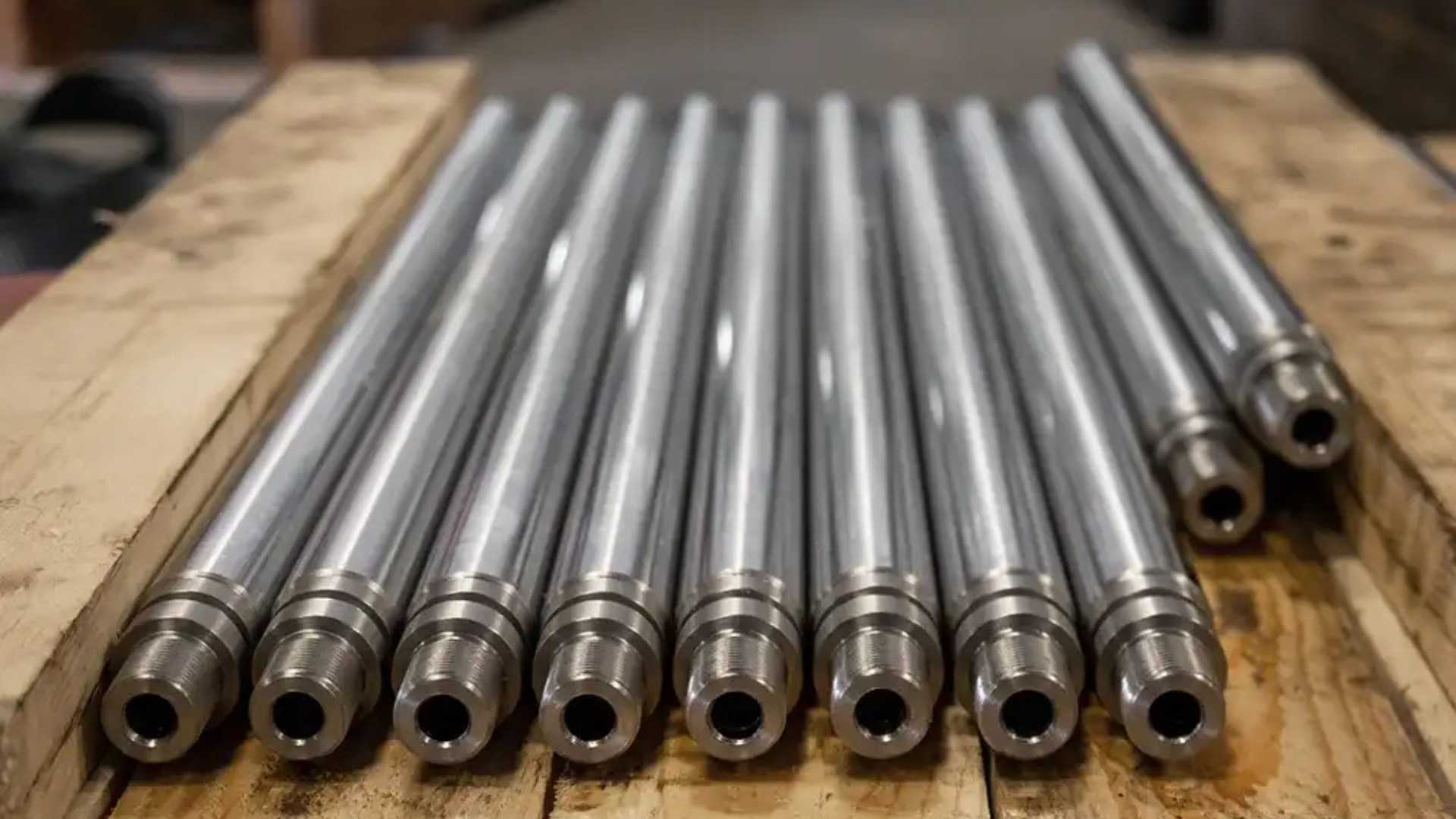
Key Considerations for Material Selection
- Load and Pressure: The primary factor is the load the cylinder rod will bear and the operating pressure of the system. High loads and pressures necessitate materials with high tensile strength and yield strength to prevent deformation.
- Wear Resistance: Cylinder rods are constantly in contact with seals and bushings, so wear resistance is vital. Materials with good wear properties minimise friction and extend the life of both the rod and the seals.
- Corrosion Resistance: Exposure to moisture, chemicals, or harsh environments requires a material that resists corrosion to maintain functionality and prevent surface degradation.
- Machinability: The ease of machining the chosen material impacts production costs and lead times. Some materials might require specialised equipment or techniques.
- Cost: Material selection often involves a balancing act between performance needs and budget constraints. High-performance materials might come at a premium cost.
Common Cylinder Rod Materials
The following table summarises some common cylinder rod materials and their strengths and weaknesses:
Additional Considerations:
- Surface Roughness: A smooth surface finish minimises friction and wear. Precision grinding or external honing is the recommended finishing process for cylinder rods.
- Rod Diameter: Larger diameter rods offer greater load-bearing capacity but might be heavier and more expensive.
Selecting the Right Surface Treatment
Surface treatments can significantly enhance the performance of a cylinder rod. Here are some common options:
- Induction Hardening: This process locally heats the surface of the rod, increasing its hardness and wear resistance while maintaining a ductile core for better impact resistance. Ideal for applications with high wear and moderate shock loads.
- Hard Chrome Plating: A thin layer of chromium is electroplated onto the rod surface, creating a very hard and wear-resistant layer with a hardness of +-76 HRc. Excellent choice for high-wear applications but requires careful control to avoid brittleness.
Choosing the Right Combination
The optimal combination of material and surface treatment depends on your specific application. For example, a hydraulic cylinder operating in a dusty environment might benefit from chrome plating, but wouldn’t need induction hardening or stainless steel. Conversely, a high-pressure application with minimal corrosion risk might utilise a hardened chrome-plated steel rod and wouldn’t benefit from stainless steel.
Honingcraft: Your Partner in Cylinder Rod Solutions
At Honingcraft, we understand the importance of selecting the right cylinder rod material and treatment. We offer a wide range of materials and surface finishing options, including honing, precision grinding to ensure your cylinder rods perform optimally. Depending on the application, we can offer between 0.1 and 0.5 μmRa surface finish.
Our team of experts can help you analyse your application requirements and recommend the best solution for your needs.
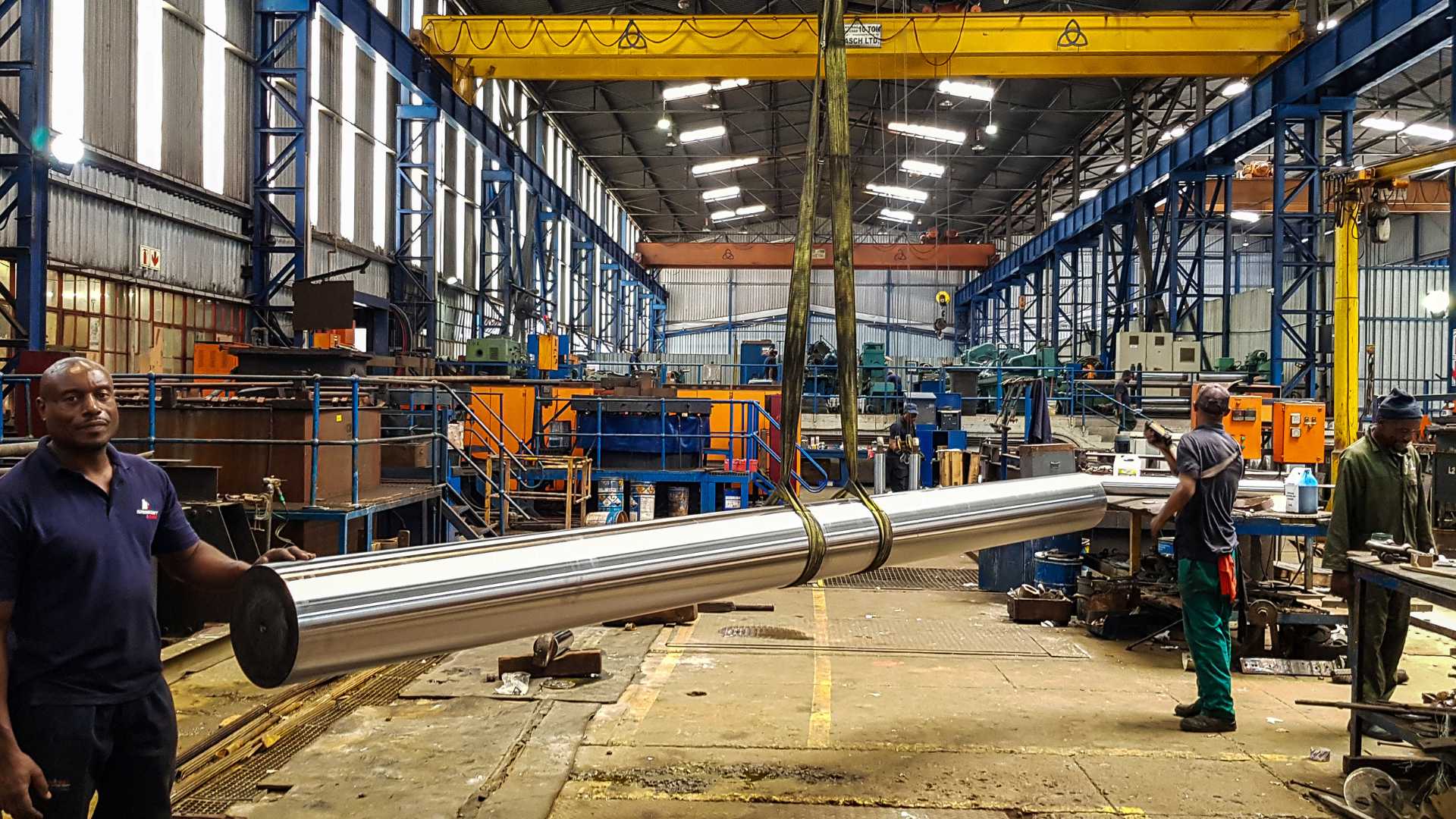
Here's how Honingcraft can help you:
- Material Selection Expertise: Our team has extensive knowledge of various cylinder rod materials and their properties. We can guide you through the selection process, considering factors like load, pressure, wear resistance, corrosion risk, and budget constraints.
- Surface Finishing Options: We offer a variety of surface finishing services, including honing, chrome plating, nickel-chromium plating, and nitriding. We can help you choose the most appropriate treatment based on your application’s specific demands.
- Custom Solutions: We understand that your needs might be unique. We can work with you to find a custom solution that meets your specific requirements.
- Quality Assurance: Honingcraft is committed to providing high-quality cylinder rods. We utilise strict quality control procedures to ensure all components meet the highest standards.
Don't settle for anything less than the best!
Contact Honingcraft today to discuss your cylinder rod needs. Our team is here to help you select the right materials and treatments to ensure your equipment.