Fluid power systems are essential in various industries, from manufacturing and construction to aerospace and automotive applications. These systems rely on fluid power circuits to transfer energy efficiently. There are two primary types of fluid power circuits: hydraulic circuits and pneumatic circuits. Understanding their differences, advantages, and applications can help businesses choose the best system for their needs.
What Are Fluid Power Circuits?
- Hydraulic Circuits – Use liquids (usually oil) to transmit power.
- Pneumatic Circuits – Use compressed air or gas for power transmission.
Comparison of Hydraulic and Pneumatic Circuits
Below is a comparison of hydraulic and pneumatic circuits based on key parameters:
Feature | Hydraulic Circuits | Pneumatic Circuits |
Medium Used | Oil or other liquids | Compressed air or gas |
Power Density | High | Lower compared to hydraulics |
Operating Pressure | Typically 1,000 – 5,000 PSI | Typically 80 – 120 PSI |
Speed Control | Precise and smooth | Less precise, high-speed operations |
Energy Efficiency | High (due to incompressibility of fluid) | Lower (air compressibility leads to losses) |
Maintenance | Requires more due to potential leaks | Easier maintenance, fewer leaks |
Application | Heavy machinery, construction, manufacturing | Automation, robotics, lightweight applications |
Hydraulic Circuits
Hydraulic circuits use pressurised liquid to transmit force. They are known for their high power density, making them ideal for heavy-duty applications that require significant force.
Components of a Hydraulic Circuit:
- Reservoir – Stores hydraulic fluid.
- Pump – Pressurises and moves the fluid.
- Valves – Control flow and pressure.
- Actuators (Cylinders or Motors) – Convert fluid energy into mechanical motion.
- Filters – Keep the fluid clean by removing contaminants.
Advantages of Hydraulic Circuits:
- Capable of handling heavy loads.
- Provides precise and smooth motion control.
- Can operate in extreme environments.
Common Applications:
- Earthmoving equipment (excavators, loaders).
- Industrial presses and injection moulding machines.
- Aircraft landing gear and control systems.
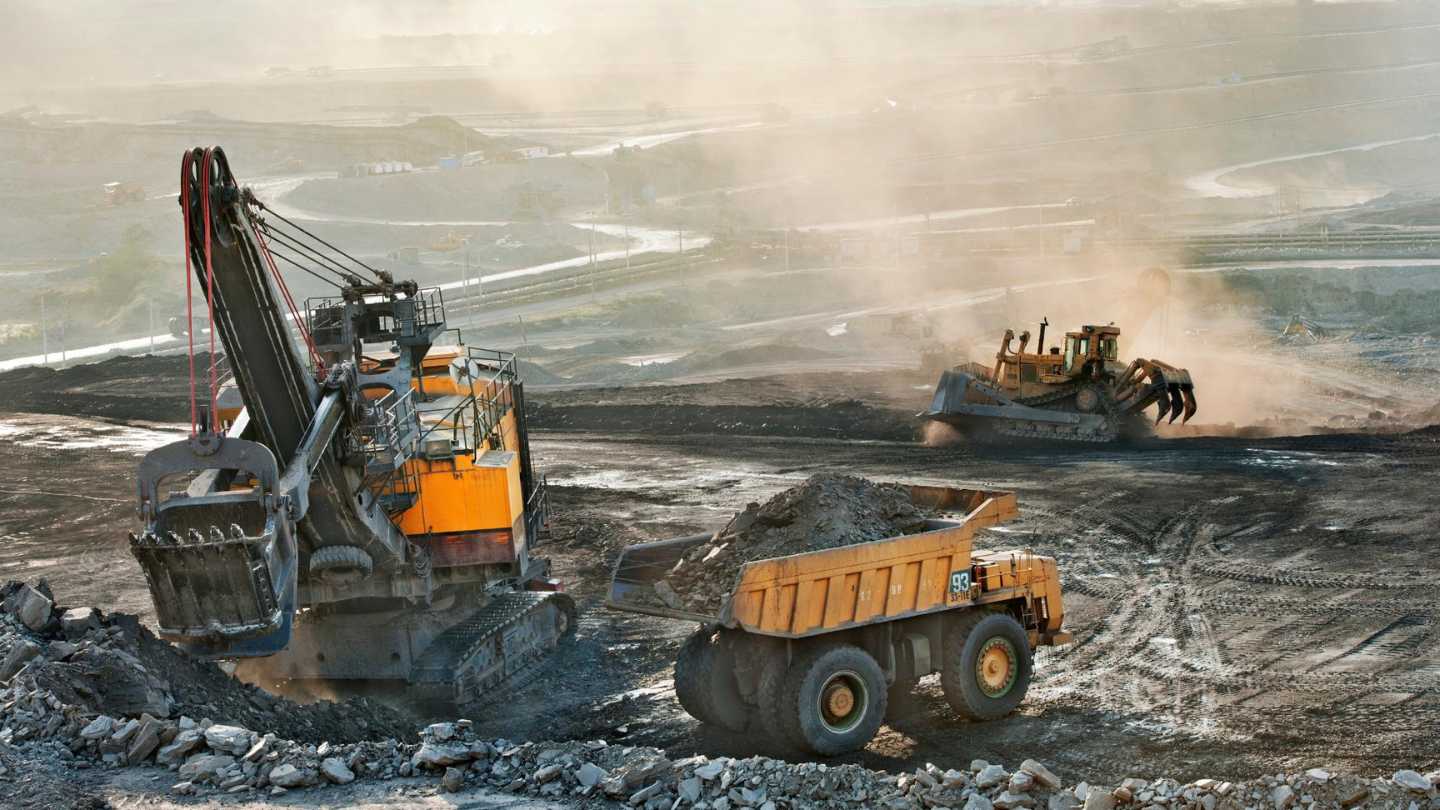
Pneumatic Circuits
Pneumatic circuits use compressed air to generate movement. These circuits are commonly used in applications requiring fast and lightweight operations.
Components of a Pneumatic Circuit:
- Compressor – Generates compressed air.
- Reservoir (Air Tank) – Stores compressed air.
- Valves – Control airflow direction and pressure.
- Actuators (Cylinders or Motors) – Convert air pressure into motion.
- Regulators and Lubricators – Maintain optimal air pressure and lubrication.
Advantages of Pneumatic Circuits:
- Clean and environmentally friendly (uses air).
- Lower initial cost and maintenance requirements.
- Safe operation in hazardous environments (no risk of fluid leaks or fire hazards).
Common Applications:
- Packaging and assembly lines.
- Automated robotic systems.
- Medical equipment and dental tools.
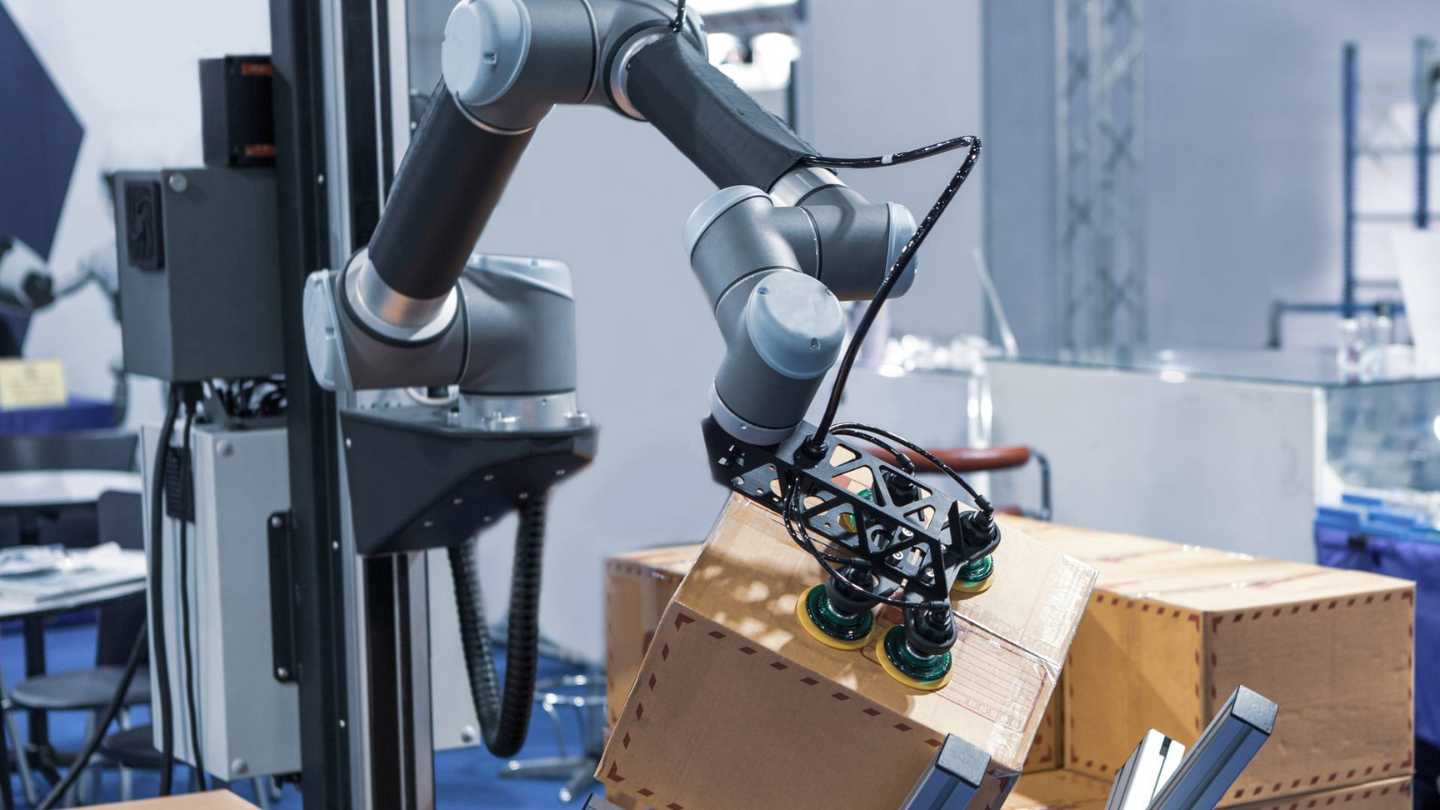
Choosing the Right Circuit for Your Application
Selecting between hydraulic and pneumatic circuits depends on factors such as power requirements, precision, cost, and operating conditions. Below is a quick guide to help with decision-making:
Requirement | Best Choice |
High force and power | Hydraulic Circuit |
Lightweight, high-speed motion | Pneumatic Circuit |
Precise motion control | Hydraulic Circuit |
Low-cost and easy maintenance | Pneumatic Circuit |
Hazardous environments | Pneumatic Circuit |
Conclusion
Both hydraulic and pneumatic circuits play a crucial role in modern industries. While hydraulic systems offer superior power and precision for heavy-duty applications, pneumatic systems provide fast, lightweight, and cost-effective solutions for automation. By understanding their differences, businesses can make informed decisions to optimise their operations. Contact Honingcraft for more industry insights!
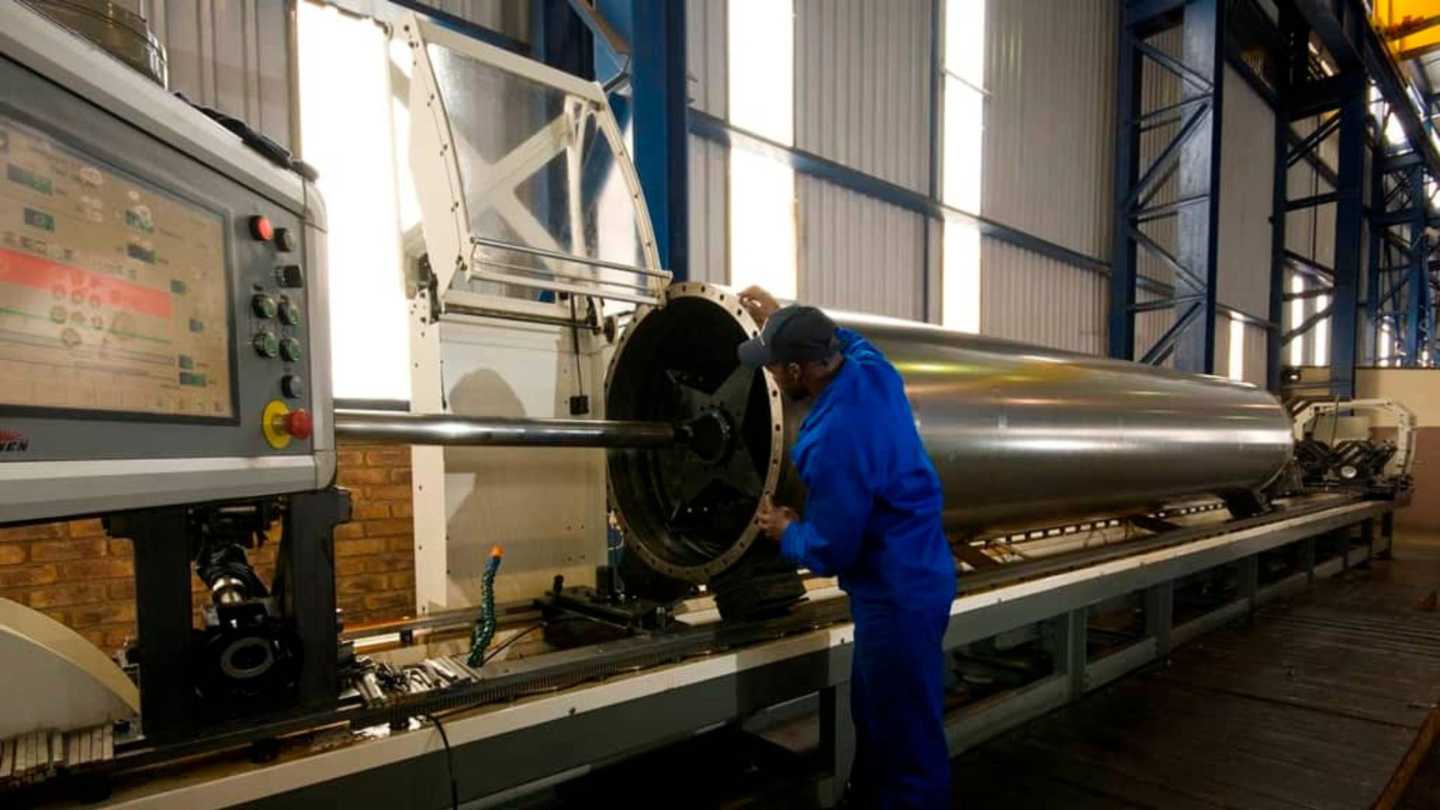
For expert solutions in honing and hydraulic system maintenance, visit Honingcraft – your trusted partner in precision engineering.