This article is part of our ongoing series on why hydraulic cylinders fail. Understanding the root causes of hydraulic cylinder failure is crucial for maximising the longevity and efficiency of your equipment. In this article, we’ll explore five critical factors that often lead to failure: under-design of cylinders, understated seals, overpowered fluid application, and injection.
Overpowered Fluid Application
Hydraulic systems rely on fluid power to operate, but when the fluid application is overpowered, it can cause significant damage to the hydraulic cylinders. Overpowered fluid application occurs when the pressure or flow rate exceeds the cylinder’s design limits. The effects of this include:
- Cylinder Rupture: Excessive pressure can cause the cylinder walls to rupture, leading to catastrophic failure.
- Seal Damage: Overpowered fluid can damage the seals, leading to leaks and reduced performance.
- Reduced Control: High fluid pressure can make it difficult to control the cylinder’s movement, leading to jerky or erratic operation.
Table 1: Risks of Overpowered Fluid Application
To prevent overpowered fluid application, it’s essential to match the hydraulic fluid specifications with the cylinder’s design parameters. This includes using the correct pressure relief valves and monitoring the system to ensure that the fluid power remains within safe limits.
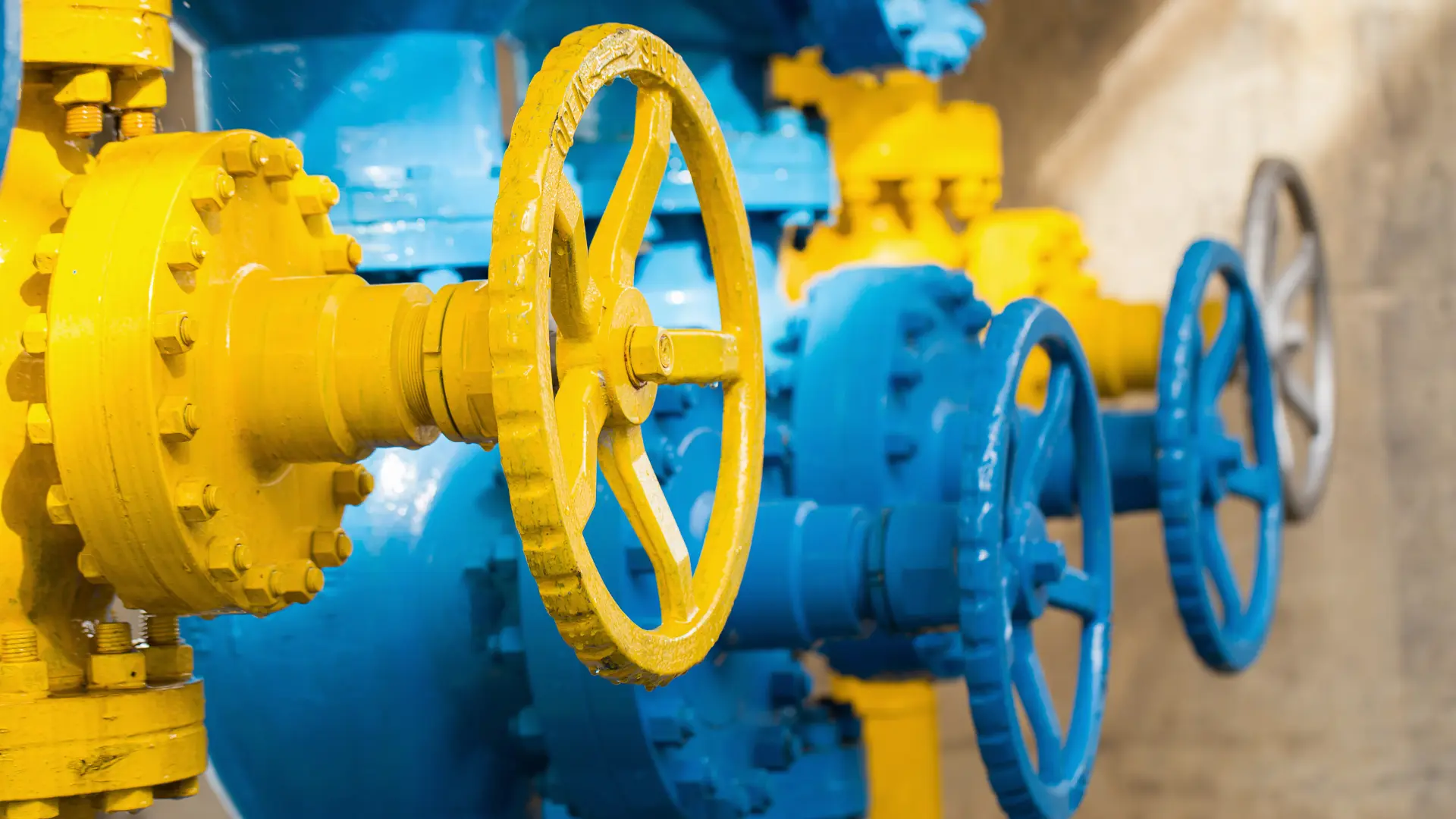
Under-design of Hydraulic Cylinders
Under-designing hydraulic cylinders is a common issue that can lead to premature failure. This occurs when the cylinder is not engineered to withstand the loads and forces it will encounter in actual operation. The consequences of under-design include:
- Increased Stress on Components: A cylinder that is not designed with sufficient strength will experience excessive stress, leading to accelerated wear and potential failure.
- Reduced Operational Efficiency: Under-designed cylinders may not perform optimally, leading to inefficiencies in the hydraulic system.
- Early Fatigue: Components that are repeatedly subjected to forces beyond their design limits will fatigue more quickly, leading to cracks and eventual failure.
Table 2: Common Symptoms of Under-designed Hydraulic Cylinders
To avoid these issues, it is essential to ensure that hydraulic cylinders are designed with the appropriate specifications for the intended application. This includes considering factors such as load capacity, pressure ratings, and material strength.
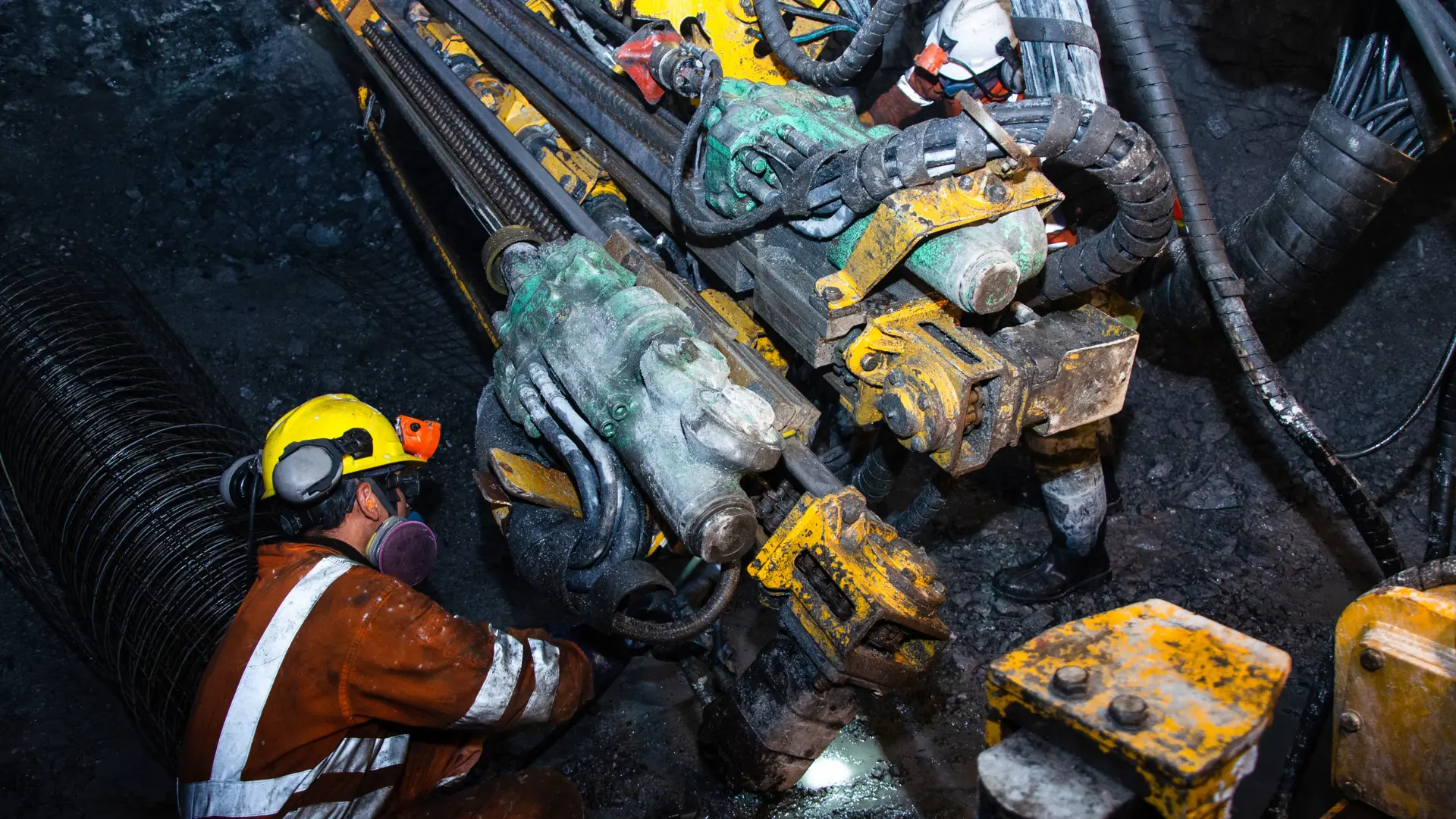
Understated Seals
Seals play a vital role in maintaining the integrity of hydraulic cylinders by preventing fluid leakage and keeping contaminants out. When seals are understated or inadequately specified, several problems can arise:
- Fluid Leaks: Insufficient sealing can lead to fluid leaks, reducing the efficiency of the hydraulic system and potentially causing environmental hazards.
- Contamination: Inadequate seals can allow contaminants to enter the cylinder, leading to abrasion, corrosion, and ultimately, cylinder failure.
- Heat Build-up: Poor sealing can cause heat build-up due to friction, which accelerates the degradation of both the seals and the cylinder components.
Table 3: Consequences of Understated Seals
Selecting the right seals for your hydraulic cylinders is critical. Consider factors such as material compatibility, operating temperature, and pressure conditions when choosing seals. Regular maintenance and inspection are also key to ensuring the seals remain in good condition.
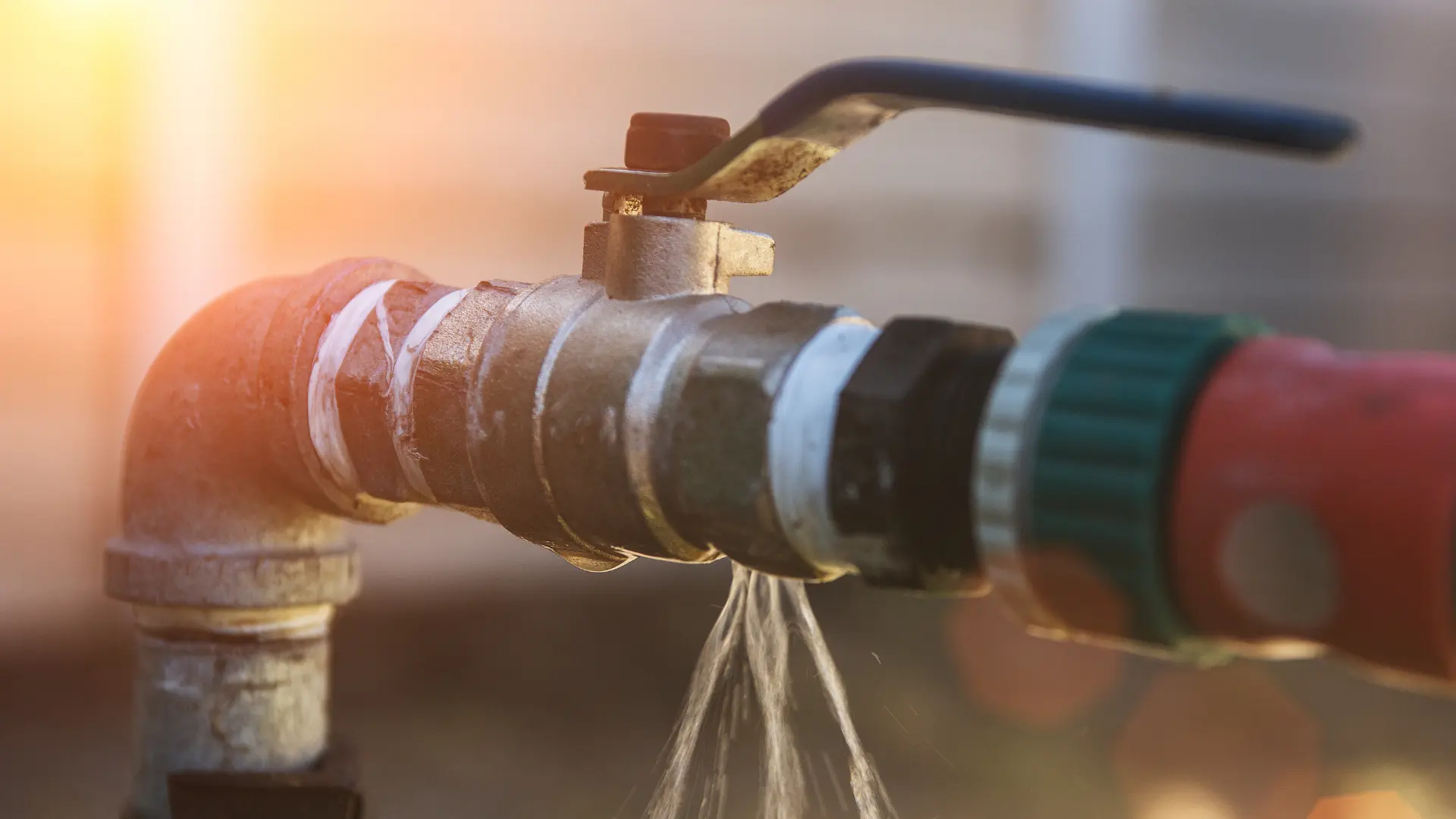
Injection
Injection is a lesser-known issue but can be just as damaging as the other factors mentioned. Injection refers to the unintended introduction of high-pressure fluid into areas of the cylinder where it shouldn’t be. This can occur due to poor design, improper maintenance, or component failure. The consequences of injection include:
- Component Erosion: High-pressure fluid can erode the internal components of the cylinder, leading to premature wear and failure.
- Severe Leaks: Injection can cause seals to blow out, leading to severe fluid leaks and system inefficiencies.
- Safety Hazards: In extreme cases, injection can cause explosive failures, posing significant safety risks to operators.
Table 4: Effects of Injection on Hydraulic Cylinders
Preventing injection requires a thorough understanding of the hydraulic system’s design and operation. Regular inspections and maintenance are critical to identifying and addressing any potential issues before they lead to failure.
conclusion
Understanding the various factors that can lead to hydraulic cylinder failure is crucial for maintaining the longevity and reliability of your hydraulic systems. By addressing issues related to under-design, understated seals, overpowered fluid application, and injection, you can significantly reduce the risk of failure and ensure that your cylinders operate efficiently and safely.
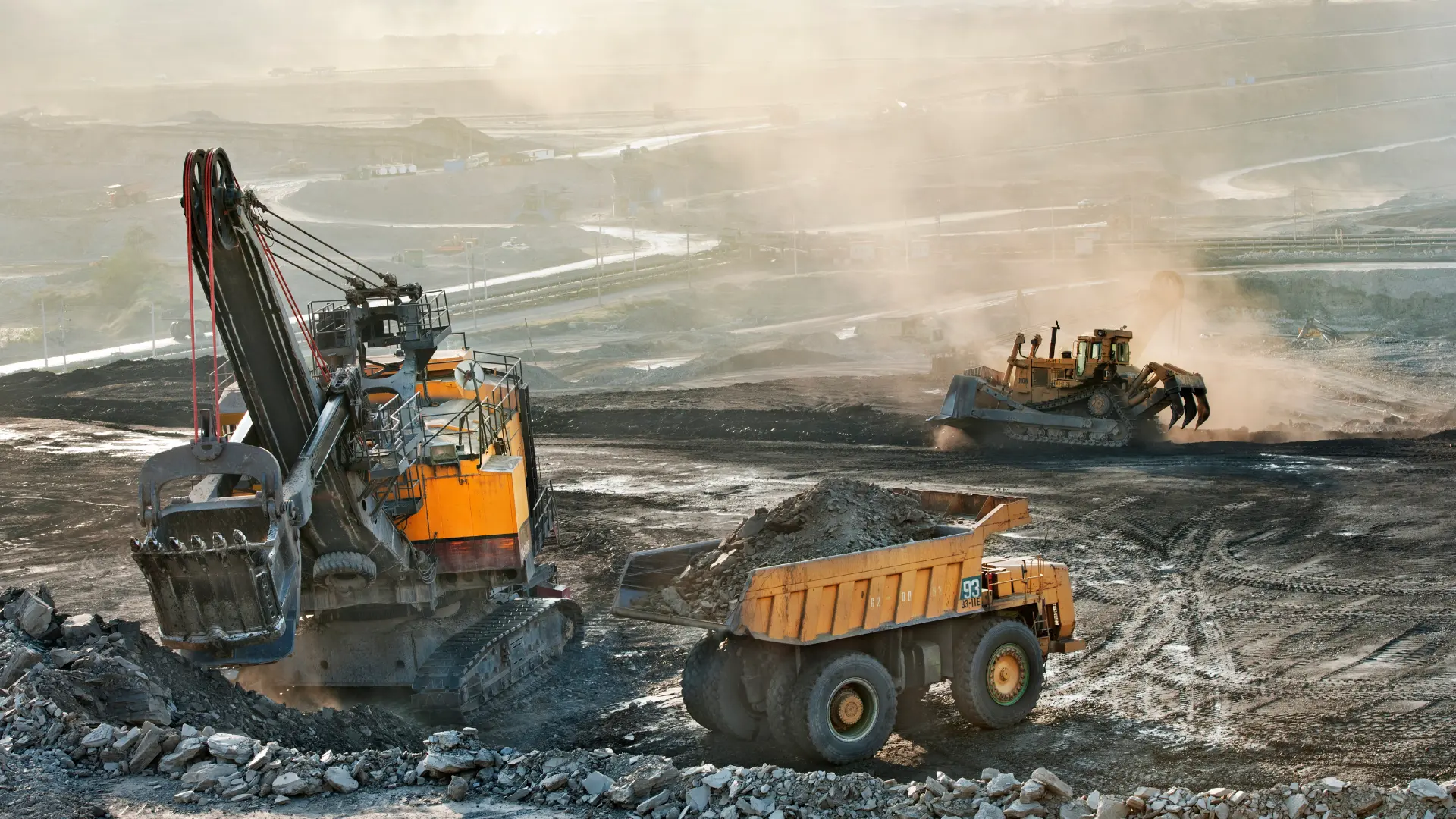
This article is part of a series on hydraulic cylinder failure, which you can find on Honingcraft’s blog. Stay tuned for our next article, where we will explore additional factors that contribute to hydraulic cylinder failure and how to mitigate them.
For expert advice and high-quality hydraulic cylinders that are designed to withstand the toughest conditions, contact Honingcraft today. Visit Honingcraft’s website to explore our full range of products and services. Whether you need custom solutions or standard components, we’re here to help you keep your operations running smoothly.